In today’s competitive marketplace, packaging plays a critical role in ensuring product safety, extending shelf life, and maintaining product integrity. Among the numerous packaging innovations, filler masterbatches have become essential in enhancing barrier properties, especially in industries where protection from external elements is crucial.
This blog will explore how filler masterbatches improve packaging’s barrier properties, ensuring the protection and longevity of products, and why they are a pivotal solution for modern packaging challenges.
What Are Filler Masterbatches?
Filler masterbatches are compounds added to packaging materials to improve their functionality and reduce the cost of production. They typically contain fillers such as calcium carbonate, talc, or other minerals, which are incorporated into plastics to improve strength, reduce production costs, and in many cases, enhance barrier properties. These materials not only improve the physical characteristics of packaging but also contribute to environmental sustainability by reducing plastic usage.
The Importance of Barrier Properties in Packaging
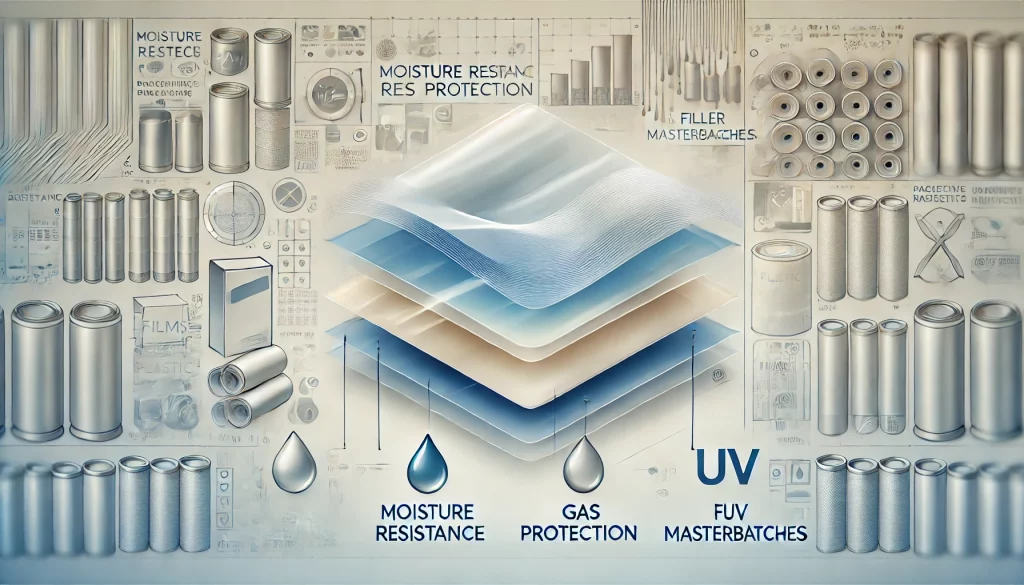
Barrier properties are the ability of packaging materials to resist the penetration of external substances such as gases, moisture, and UV light. These properties are vital for maintaining product quality, especially in industries like food and pharmaceuticals, where contamination or degradation could lead to serious consequences.
By enhancing these properties, masterbatches help to protect products from environmental factors, ensuring they reach the consumer in optimal condition. Improved barrier properties can help extend the shelf life of perishable products, reduce spoilage, and maintain the integrity of the contents.
How Filler Masterbatch Enhance Barrier Properties
Filler masterbatches are critical in optimizing packaging performance. Here’s how they contribute to enhancing the barrier properties of packaging materials:
1. Moisture Resistance
One of the most important barriers in packaging is resistance to moisture. In many industries, such as food and pharmaceuticals, controlling moisture levels is key to preserving product quality. Filler help improve the material’s resistance to moisture by filling the polymer matrix, reducing the permeability of water vapor through the packaging.
2. Gas Barrier Enhancement
In applications where preventing the permeation of gases like oxygen or carbon dioxide is crucial, filler masterbatches act as a shield, reducing the transmission rate of gases. This is especially important in food packaging, where oxidation can lead to spoilage. Filler masterbatches help create a denser structure within the packaging material, slowing down the movement of gases and thus improving product longevity.
3. UV Protection
Many products, particularly pharmaceuticals and cosmetics, are sensitive to light exposure. UV radiation can degrade the quality of products over time, causing them to lose efficacy or spoil. Masterbatches can be customized to block harmful UV rays, enhancing the light barrier properties of the packaging. This ensures that the products inside are protected from UV damage, preserving their quality and extending their shelf life.
4. Mechanical Strength for Better Protection
Masterbatches improve the mechanical strength of packaging materials, making them more durable and resistant to wear and tear during transportation and handling. Stronger packaging ensures that the barrier properties remain intact, preventing any leaks or contamination from external factors.
Cost Efficiency with Filler Masterbatches
In addition to enhancing barrier properties, filler masterbatches offer significant cost benefits to manufacturers. By replacing a portion of the plastic with inexpensive fillers, manufacturers can reduce the overall material costs without sacrificing the protective properties of the packaging.
Moreover, the enhanced barrier properties provided by filler masterbatches can reduce the need for additional protective layers in the packaging, further cutting down production costs. This makes them an efficient and economical solution for industries looking to optimize packaging performance while maintaining cost-effectiveness.
Sustainability and Filler Masterbatches
Sustainability is a growing concern across industries, and packaging is no exception. By incorporating filler masterbatches into packaging materials, manufacturers can reduce the overall amount of plastic used, contributing to more eco-friendly packaging solutions. Filler masterbatches allow for thinner packaging materials without compromising on strength or barrier properties, which reduces plastic waste and the environmental footprint of packaging.
Choosing the Right Filler Masterbatch for Your Packaging
When selecting a filler masterbatch, it’s important to consider the specific barrier requirements of your packaging. Different products require different levels of protection, whether it’s moisture resistance, gas barrier protection, or UV shielding.
Consulting with an expert in filler masterbatches can help you choose the right combination of materials to meet your packaging needs. Whether you’re looking to extend the shelf life of perishable products or protect sensitive goods from environmental factors, filler masterbatches offer a versatile and customizable solution.
Conclusion:
In an increasingly competitive market, ensuring that your products are protected from external threats is more important than ever. Filler masterbatches offer a cost-effective and efficient way to enhance the barrier properties of your packaging, safeguarding your products from moisture, gases, UV rays, and mechanical damage.
If you’re looking to improve your packaging performance, reduce costs, or explore more sustainable options, filler masterbatches can provide the solution. Take your packaging to the next level with optimized barrier properties that protect your products and your brand.
Get in touch with us today to learn how filler masterbatches can revolutionize your packaging solutions.