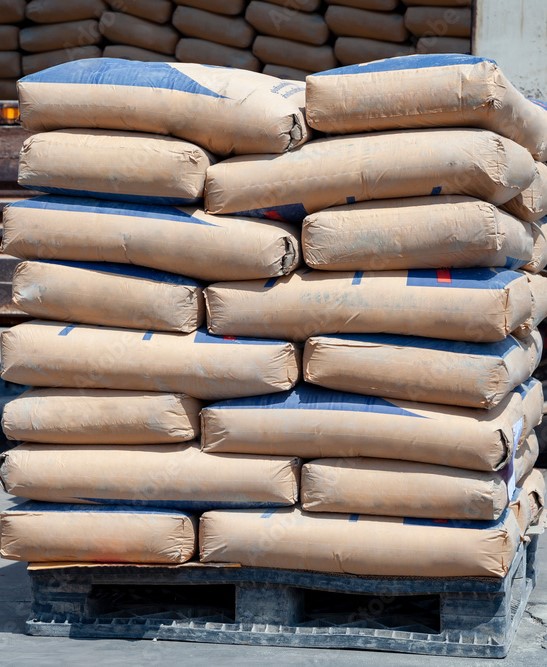
Cement Bags
The construction industry relies heavily on cement bags because they are a safe and practical way to carry and store the material. Many cement bag manufacturers in India cater to the building industry’s requirements. These bags can resist the wear and tear of being stored, handled, and transported without compromising the cement.
Bags used to transport cement from the plant to the job site are vital to the cement’s continued viability and freshness. They are built to last and designed with safety and efficiency in mind so that glue may be moved about with little risk of injury. Cement bags may be tailored to the specific needs of the construction industry by offering a wide range of alternatives in terms of size, weight capacity, and personalization.
Strength and Density of Cement Bags
Their strength and density may broadly gauge the quality and longevity of cement bags. To guarantee that cement bags can survive the construction sector’s storage, handling, and transportation demands, it is essential to have a firm grasp of their strength and density properties. Here’s the lowdown on cement bag tensile strength and density :
- Strength of Cement Bags : Cement bag strength is measured by the bag’s resistance to ripping or bursting when subjected to force. The loads must be strong enough to handle the cement’s weight and pressure and the external forces experienced during transport and storage. Cement bags undergo stringent quality control techniques, such as burst testing and tensile strength tests, to ensure their durability. By measuring the bag’s resistance to pressure and ripping, these tests guarantee that it can securely hold and carry cement without rupturing during transit, as industry requirements require.
- The density of Cement Bags : Cement bag density is the mass or weight of a bag relative to its volume. It’s a factor in the bags’ total carrying and storing capacities. A bag’s density is affected by its construction materials, as well as its thickness and stacking. The strength-to-weight ratio of cement bags is carefully calculated. The bags must be durable, yet they should be manageable to carry. This guarantees economical and efficient shipping and handling.
Manufacturers of cement bags pay close attention to the bags’ densities throughout production to get the best possible results. Woven polypropylene or paper is utilized because it is strong enough to meet specifications and lightweight sufficient to transport and store easily.
Manufacturing Process
Several stages are involved in making cement bags that guarantee you’ll have sturdy bags that can safely hold your cement. The standard production procedure is described below.
- The first step in making the bags is picking out the materials that would work best. Paper and woven polypropylene (PP) are two common choices. Cement storage and transport necessitate these materials due to their strength, durability, and protective qualities.
- Woven polypropylene bags are made by melting the desired polypropylene resin and extruding it into long, continuous threads. The bag’s foundation will be woven from these threads.
- The extruded polypropylene strands are woven into cloth using looms and other weaving equipment. The cement bag’s primary body is made of this cloth. The bag’s strength and longevity are guaranteed by the weaving method, which securely interlocks the strands.
- After the bag fabric has been woven, it may be printed. The manufacturer may personalize the bags by printing the company’s name, logo, product data, etc. This printing gives the bags a recognizable brand identity and efficiently promotes the products inside.
- Woven polypropylene bags may be laminated (optional) for added durability. The fabric is coated with a thin plastic film, making the backpack more resilient to rain, punctures, and other environmental hazards. Lamination protects against wear and tear, extending the bags’ life and improving functionality.
- After the bags have been weaved and printed, they are cut into individual bag panels and then stitched together. The cement bag is completed when these sections are put together with high-quality threads, commonly done using reinforced stitching methods. The bag’s structural integrity and the prevention of cement leakage depend on the quality of the stitching.
- Strict quality control procedures are used throughout the production process. The integrity, durability, and dimensional precision of sample bags are evaluated. These tests verify the bags’ compliance with industry requirements and their optimum performance during storage and transit.
Cement Bag Applications and Advantages
Cement bags have several applications and advantages in the building trade. Let’s talk about the benefits and applications of cement bags:
Uses of Cement Bags
- Cement bags are made to store cement from cement plants to building sites safely. They’re an easy and trustworthy option for preserving cement’s quality and freshness during transportation.
- Cement bags are lightweight and uniform in size, making them simple to transport and move about a job site. They’re designed to be user-friendly so employees can load, unload, and move them quickly and easily. The bags make work easier and safer by reducing the need for heavy lifting.
- Cement bags are made to be stacked vertically, which reduces the amount of floor space needed to store them. Because of their regular dimensions can be stored neatly and efficiently, freeing up significant space on building sites and storage facilities. When working with a considerable number of cement bags, this is very crucial.
Benefits of Cement Bags
- Cement bags are a barrier, shielding the cement from atmospheric moisture and other potential pollutants. This prevents any deterioration in the cement’s quality or integrity from the effects of water or impurities.
- Cement bags aid in reducing waste by keeping the material contained. They lessen the possibility of cement spoiling in storage or accidentally mixing with other substances on the road. This keeps the cement in good working condition and reduces the need to buy more or throw away unused glue.
- Cement sacks provide an excellent medium for advertising your company’s name. The manufacturers may personalize the bags by printing their logos, company names, and other information. This raises the profile of their brand, which ultimately benefits their sales.
- Cement bags are made to conform to all applicable regulations and industry specifications. They go through several checks for quality and safety to guarantee they meet all requirements. If you want to comply with the rules, you need to get cement bags from a reliable manufacturer.
- Regarding ecology, some producers provide choices like biodegradable cement sacks. These bags help with sustainability since they lessen the damage done by garbage. They are congruent with environmentally friendly activities and ethical behavior.
Factors to Consider Before Buying Cement Bags
There are a number of things to keep in mind when shopping for cement bags for building projects to ensure you get the ideal bags for your needs. Before you go out and purchase bags of cement, you should think about these things.
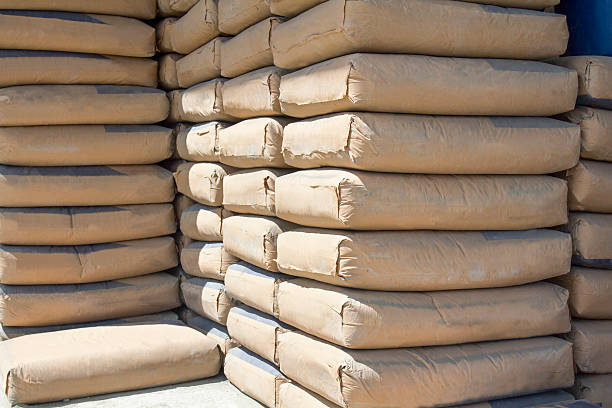
- Dimensions and Load Limits : Consider your project’s demands while deciding on the bag size and capacity. Choose cement bags that are large enough to hold the required quantity of cement yet small enough to fit within the site’s logistical limits.
- Choices for Printing and Logos : Examine the choices for imprinting your company’s logo, brand name, or other pertinent information on the bags. Promoting your construction company and raising brand awareness with personalized printing is a win-win.
- Method of Closure : The cement’s freshness and quality may be preserved and prevented from degrading during storage and transit if you use self-sealing or stitched closures.
- Cost-effectiveness : Consider the quality of the bags, the availability of personalization choices, and any extra services each vendor gives when comparing their rates. Strive for a middle ground between price and quality to get the most out of your money.
- Adherence to Professional Practices : Ensure the bags meet all safety, quality, and environmental sustainability criteria. Pick bags made by companies with a good track record for adhering to standards and conducting quality assurance testing.
Conclusion
Cement bags provide a dependable method of storing and transporting cement, making them an essential part of the building industry. Cement bags of varying sizes, strengths, and individualization choices are all available from Indian manufacturers. These bags help with brand marketing and regulatory compliance while protecting, preserving, and efficiently using cement. Choosing the correct cement bags for construction projects requires careful consideration of elements such as bag strength, bag size, printing possibilities, and compliance with requirements.