Woven polypropylene bags are widely used in industries such as agriculture, chemicals, construction, and retail. Their durability, cost-effectiveness, and versatility make them an excellent choice for packaging. However, one crucial aspect of manufacturing woven bags is the cutting method. Two common techniques used in the industry are blade cutting and heat cutting. Each has its own advantages, limitations, and best-use cases.
In this blog post, we’ll explore the differences between these two techniques, their applications, and how to choose the right one for your needs.
Understanding the Basics of Woven Bag Cutting
The cutting process is an essential step in the production of woven bags. It ensures that the bags are of uniform size, have clean edges, and are prepared for further processing, such as stitching or printing. The choice between blade cutting and heat cutting depends on factors like the type of material, production requirements, and end-use.
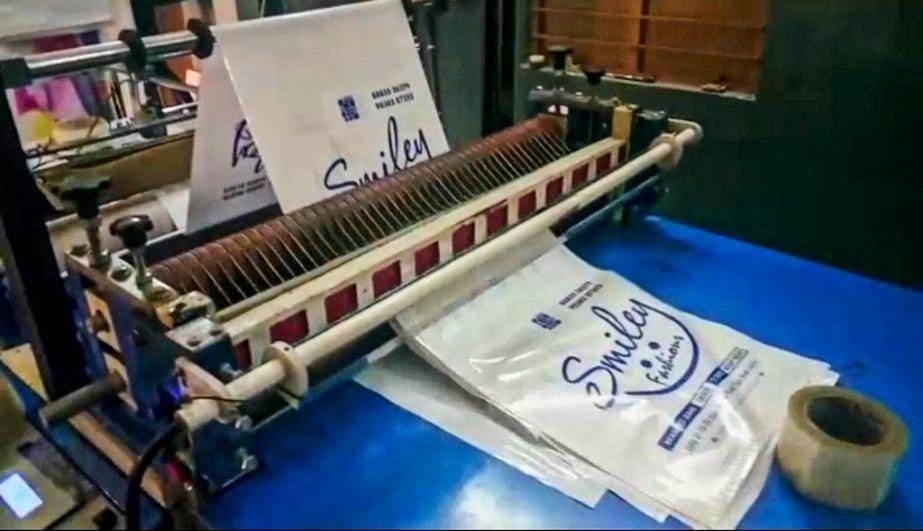
Before diving into the comparison, let’s take a closer look at each technique.
What is Blade Cutting?
Blade cutting is a mechanical method that uses a sharp blade to cut woven polypropylene fabric. It is a straightforward and traditional technique, often preferred for its simplicity and speed.
What is Heat Cutting?
Heat cutting, on the other hand, involves using a heated blade or thermal cutter. This method not only cuts the fabric but also seals the edges simultaneously, preventing fraying and unraveling.
Key Differences Between Blade and Heat Cutting
While both techniques achieve the same goal—cutting the material—they differ in process, outcomes, and applications. Let’s break it down.
1. Cutting Precision
- Blade Cutting: Offers clean and precise cuts. It’s highly effective for cutting straight edges and is suitable for applications where precision is critical.
- Heat Cutting: Provides precise cuts while simultaneously sealing the edges. It’s particularly useful for materials prone to fraying, such as woven polypropylene.
2. Edge Sealing
- Blade Cutting: Does not seal edges, which can lead to fraying over time. This is a significant drawback, especially for bags intended for heavy or long-term use.
- Heat Cutting: Seals edges as it cuts, ensuring durability and preventing fraying. This feature makes it ideal for products requiring high-quality finishes.
3. Speed and Efficiency
- Blade Cutting: Faster than heat cutting, especially for high-volume production. The simplicity of the mechanism allows for quick processing.
- Heat Cutting: Slightly slower due to the additional edge-sealing process. However, the quality and durability of the output often justify the extra time.
4. Cost Implications
- Blade Cutting: Generally more cost-effective due to the simplicity of the equipment and lower energy requirements.
- Heat Cutting: Requires more expensive equipment and consumes more energy, making it a costlier option in terms of initial investment and operational expenses.
Advantages and Disadvantages of Each Technique
To choose the right cutting method for your woven bags, it’s essential to weigh the pros and cons of each technique.
Advantages of Blade Cutting
- Cost-Effective: Lower equipment and operational costs make it suitable for budget-conscious operations.
- High Speed: Ideal for large-scale production with minimal downtime.
- Simplicity: Easy to set up and operate, requiring less technical expertise.
Disadvantages of Blade Cutting
- Fraying Edges: May require additional steps, such as hemming or sealing, to prevent fraying.
- Limited Use Cases: Not suitable for products where edge durability is critical.
Advantages of Heat Cutting
- Edge Sealing: Ensures a professional finish and prevents fraying.
- Durability: Makes the bags more robust and long-lasting.
- Versatility: Suitable for a wide range of applications, including high-quality packaging.
Disadvantages of Heat Cutting
- Higher Cost: Both equipment and energy consumption are more expensive.
- Slower Speed: The additional sealing process can slow down production.
Applications of Blade and Heat Cutting
Different industries and use cases call for specific cutting techniques. Here’s how these methods are typically applied:
Blade Cutting Applications
- Temporary Packaging: Ideal for bags used for short-term storage or transportation.
- Budget Packaging Solutions: Suited for businesses that prioritize cost over durability.
- Straightforward Designs: Used when the material doesn’t require edge sealing, such as for some agricultural products.
Heat Cutting Applications
- Heavy-Duty Packaging: Perfect for products like sand, cement, or fertilizers, where durability is essential.
- Custom Designs: Suitable for branded or printed bags that require a polished look.
- Long-Term Use: Ideal for reusable bags or products exposed to rough handling.
Choosing the Right Technique for Your Needs
Selecting the appropriate cutting method depends on various factors. Here’s a guide to help you decide:
1. Consider the Material
- For woven polypropylene or materials prone to fraying, heat cutting is a better choice.
- For materials that don’t require edge sealing, blade cutting suffices.
2. Assess the Budget
- If cost is a primary concern, blade cutting offers a more economical solution.
- If you’re willing to invest in higher quality, heat cutting provides long-term value.
3. Evaluate Production Volume
- For high-volume production with tight deadlines, blade cutting is faster and more efficient.
- For smaller batches where quality is prioritized, heat cutting is worth the extra time.
4. Think About the End-Use
- For disposable or temporary bags, blade cutting is adequate.
- For durable, reusable, or branded bags, heat cutting delivers superior results.
Future Trends in Woven Bag Cutting
Advancements in technology are continually improving the efficiency and effectiveness of cutting methods. Automation is playing a significant role, with machines that combine the speed of blade cutting with the precision of heat sealing. These hybrid solutions are likely to become more popular as industries demand both quality and efficiency.
Additionally, the growing focus on sustainability is encouraging manufacturers to explore cutting methods that reduce waste and energy consumption. Heat cutting, for instance, minimizes material loss by sealing edges, making it an eco-friendly option despite its higher energy requirements.
Conclusion
When it comes to choosing between blade and heat cutting for woven bags, there’s no one-size-fits-all answer. Each technique has its strengths and weaknesses, and the right choice depends on your specific needs, including material type, budget, production volume, and end-use.
Blade cutting is a cost-effective and speedy option for basic applications, while heat cutting offers superior edge sealing and durability for high-quality products. By understanding the nuances of each method, you can make an informed decision that ensures your woven bags meet both functional and aesthetic requirements.
Whether you’re looking to enhance your production line or explore new packaging solutions, selecting the right cutting technique is a critical step toward achieving your goals.