In the ever-evolving world of packaging, Flexible Intermediate Bulk Containers (FIBC) bags have become essential for transporting and storing bulk materials across a range of industries. From agriculture to chemicals, FIBC bags are trusted for their versatility, strength, and cost-efficiency. As businesses increasingly demand smarter, more sustainable, and durable packaging solutions, the design and technology behind FIBC bags have undergone significant innovations. This blog post will delve into the latest advancements in FIBC bag design and technology and explore how these innovations are transforming the packaging industry.
The Evolution of FIBC Bags: From Standard to Smart Packaging
FIBC bags, also known as jumbo bags or bulk bags, store and transport dry, flowable materials like grains, chemicals, sand, or fertilizers. Historically, manufacturers made these bags from woven polypropylene (PP), offering strength, flexibility, and resistance to harsh conditions. However, as the demands of modern industries increased, FIBC bags have evolved to meet new challenges.
Today, FIBC bags feature new designs and technologies that enhance their safety, efficiency, and sustainability.
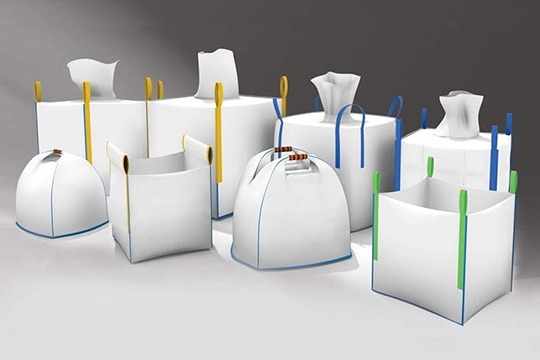
The Drive for Innovation
As industries focus more on efficiency, sustainability, and safety, FIBC bags have incorporated innovative features. These innovations improve packaging, enhance the bags’ functionality, and meet rising expectations in business and consumer markets. These advancements address growing needs in logistics, waste management, and environmental conservation.
Key Innovations in FIBC Bag Design
The design of FIBC bags has evolved significantly, incorporating advanced features that enhance their strength, durability, and functionality. These key innovations are driving improvements in packaging efficiency, sustainability, and safety across various industries.
1. Enhanced Strength and Durability
One of the most significant innovations in FIBC bags is the development of stronger, more durable materials. Historically, manufacturers primarily made FIBC bags from woven polypropylene. Although this material was suitable for most applications, recent developments have led to the introduction of stronger materials and new manufacturing techniques.
High-Density Polyethylene (HDPE) and Laminated FIBC Bags
The adoption of high-density polyethylene (HDPE) in FIBC bags has provided a significant upgrade in packaging technology. HDPE offers greater tensile strength and resistance to damage from abrasion and weather conditions compared to traditional polypropylene. Additionally, laminated FIBC bags now include a layer of polyethylene film between the woven fabric, improving strength and protecting against moisture, dust, and water. These innovations allow FIBC bags to handle heavier loads and reduce the likelihood of rupture or tear during transport or storage.
2. Smart FIBC Bags with RFID Technology
In today’s fast-moving logistics environment, real-time tracking and inventory management are essential. To meet this demand, manufacturers are equipping FIBC bags with Radio Frequency Identification (RFID) technology.
How RFID Enhances FIBC Bags
RFID technology enables the real-time tracking of FIBC bags. Embedded RFID tags allow businesses to monitor the movement of goods inside the bags from the warehouse to their final destination. This innovation minimizes human errors, streamlines inventory management, and provides valuable data for logistics operations.
With RFID-enabled FIBC bags, companies can track bag usage, monitor damage, and even predict the bags’ lifespan. This level of visibility improves quality control and helps companies make more informed packaging decisions.
3. Increased Sustainability in FIBC Bags
As businesses and consumers push for more sustainable practices, FIBC bags have adopted new innovations to minimize their environmental impact.
Recyclable and Biodegradable Materials
Manufacturers now use recyclable polypropylene and biodegradable polymers to produce FIBC bags. These eco-friendly materials help reduce waste and ensure the bags are reusable or can be disposed of responsibly. For example, FIBC bags made from post-consumer recycled (PCR) polypropylene lower the demand for virgin plastic, thus reducing the carbon footprint.
Additionally, bio-based polymers derived from renewable resources like corn or sugarcane are being used, further enhancing the sustainability of FIBC bags without sacrificing strength and flexibility.
Eco-Friendly Coatings
New biodegradable coatings are replacing traditional, toxic coatings used on FIBC bags. These eco-friendly coatings offer better water resistance and durability while remaining environmentally responsible. This innovation helps keep packaging safe and functional without harming the planet.
4. Customizable Features for Diverse Industries
Every industry has unique needs when it comes to bulk packaging. In response, FIBC bags have become more customizable in both design and functionality.
Specialized FIBC Bags for Different Applications
Manufacturers now tailor FIBC bags for specific uses across industries like food, chemicals, agriculture, and construction. Food-grade FIBC bags, for example, are made from FDA-approved polypropylene and come with liners or coatings to prevent contamination. This ensures the safe transportation of edible products.
In the chemical and pharmaceutical industries, anti-static FIBC bags have become essential. These bags prevent the buildup of static electricity, minimizing the risk of fires or explosions when transporting flammable materials. These innovations significantly improve safety.
Liner Options for Better Containment
Adding liners to FIBC bags has been another valuable design innovation. Liners provide additional protection for moisture-sensitive materials and fine powders. They also offer enhanced containment for hazardous materials, providing a secure barrier against leaks or spills.
5. Improved Safety Features for Handling and Transport
Ensuring the safety of workers and the integrity of the materials inside FIBC bags is a priority. As a result, safety features have been integrated into FIBC bag designs.
Safety Testing and Certifications
FIBC bags are now subjected to rigorous testing to meet industry safety standards. Manufacturers test various aspects such as load-bearing capacity, tensile strength, and puncture resistance. Bags for specific industries, such as food or chemicals, must also comply with safety regulations. This testing ensures that FIBC bags are fit for their intended purpose and meet the highest safety standards.
Future Trends in FIBC Bag Technology
As technology continues to evolve, the future of FIBC bags looks promising. Advancements in materials science, automation, and sustainability will likely lead to even more innovative solutions in the FIBC bag industry. For instance, automation in the manufacturing process could lead to more precise, customized bags, improving production efficiency. Moreover, as demand for eco-friendly solutions rises, biodegradable and recyclable FIBC bags may become the norm.
Conclusion
The design and technology behind FIBC bags have seen remarkable progress, enhancing their strength, durability, sustainability, and functionality. As industries continue to prioritize efficiency, safety, and environmental responsibility, FIBC bags are evolving to meet these demands. Innovations such as RFID technology, eco-friendly materials, and customizable designs are making FIBC bags smarter, stronger, and more sustainable. These improvements ensure that FIBC bags will continue to be a vital part of the packaging landscape, offering businesses an efficient and reliable solution for bulk storage and transportation.