Block bottom bags, often referred to as square bottom bags or Ad Star Bags, are an essential type of packaging used in various industries, including food, agriculture, and retail. These bags offer a stable base, allowing them to stand upright and provide excellent protection for products during storage and transportation. In India, the manufacturing process of block bottom bags has evolved significantly over the years, driven by advances in technology, growing demand for sustainable packaging, and a focus on innovation. This blog explores the intricate process behind the creation of block bottom bags, providing insights from Indian producers.
Understanding Block Bottom Bags
Before diving into the manufacturing process, it’s important to understand what block bottom bags are and why they are widely used across industries. A block bottom bag is a type of paper or plastic bag with a square-shaped base that allows it to stand upright. These bags are typically used for packing products such as flour, rice, pet food, and chemicals. They are preferred for their stability, ease of handling, and ability to hold more weight without breaking.
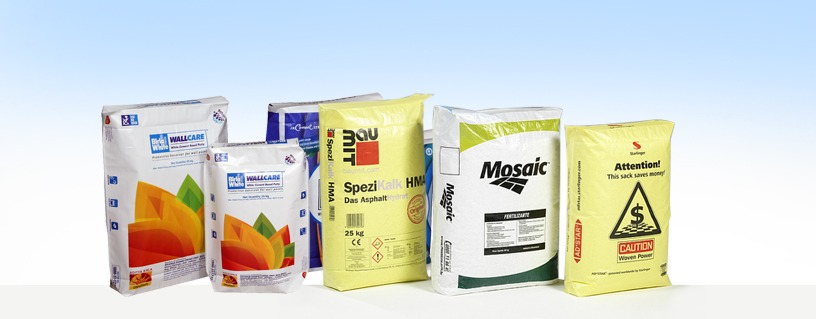
The unique block bottom design is particularly beneficial in improving product visibility on shelves and providing a solid foundation for stacking in warehouses or transportation.
Raw Materials Used in Block Bottom Bag Manufacturing
The manufacturing of block bottom bags begins with the selection of raw materials. These materials are chosen based on the intended use of the bag, product requirements, and desired strength. The two main materials used in the production of block bottom bags in India are:
Paper
For eco-friendly packaging, paper is often used for block bottom bags. Paper is biodegradable and can be easily recycled, making it a preferred choice for sustainable packaging. Kraft paper, which is durable and strong, is commonly used in the production of block bottom bags. This type of paper is made from wood pulp and is often used for food packaging due to its ability to provide excellent protection against moisture and air.
Plastic
Plastic block bottom bags are often made from polyethylene or polypropylene films. These materials are lightweight, durable, and offer resistance to moisture and chemicals. Plastic block bottom bags are widely used in industries such as chemicals, fertilizers, and pet food, where the bags need to withstand rough handling and exposure to external elements.
Composite Materials
Some producers opt for composite materials, which are a combination of paper and plastic. These hybrid bags provide the best of both worlds, offering the strength of paper and the moisture resistance of plastic. Composite block bottom bags are increasingly becoming popular for packaging a wide range of products.
The Manufacturing Process of Block Bottom Bags
The manufacturing process of block bottom bags involves several steps, each critical to ensuring the bags are strong, durable, and functional. Here is an in-depth look at the steps involved in producing these bags:
1. Material Preparation
The first step in manufacturing block bottom bags is preparing the raw materials. For paper bags, rolls of Kraft paper are sourced, and for plastic bags, plastic films are obtained from suppliers. In some cases, composite materials are prepared by laminating paper with a thin layer of plastic.
During this phase, the material is inspected for quality, ensuring that it meets the required specifications for strength and durability. Additionally, any special features such as moisture resistance or printing needs are also addressed.
2. Printing
Printing on block bottom bags is an essential part of branding and marketing. Most manufacturers in India use flexographic printing or rotogravure printing techniques to print logos, product information, and other details on the surface of the bags.
In the case of flexographic printing, the material is passed through a machine that uses flexible printing plates to transfer ink onto the surface. This printing process is fast and allows for high-quality, vibrant designs on the bags. For higher-end designs or detailed graphics, rotogravure printing is often employed. It is a high-quality process that allows for precise image reproduction on large volumes of bags.
3. Cutting and Shaping
Once the material is printed, it is fed into a cutting machine. The cutting process involves measuring and cutting the material into the required size and shape. For block bottom bags, this step is crucial as the base of the bag needs to be squared and the sides folded to create the bag’s block bottom structure.
The machine cuts the material into rectangular sheets and then shapes the sheets into a pre-determined size that aligns with the desired bag specifications. The cuts are made with precision to ensure that each bag has consistent dimensions.
4. Bottom Forming and Folding
The defining characteristic of block bottom bags is the square base, which provides stability. In this step, the bottom of the bag is formed. The rectangular sheets are folded in a way that allows them to create a block bottom.
The paper or plastic material is folded at the base, and the corners are sealed using heat or glue. The block bottom is then pressed to ensure it remains square and provides a stable, firm base for the bag. For paper bags, the folds are secured using a combination of heat and adhesive, whereas plastic bags are typically sealed using a heat-sealing method.
5. Side Sealing and Closure
After the bottom has been formed, the sides of the block bottom bag are sealed. For paper bags, a folding process is used to create the side seams, which are then glued or stitched together. For plastic bags, the sides are sealed using a heat-sealing process, ensuring that the edges are tightly bound.
At this stage, the bags are also equipped with a closure mechanism, such as a fold-over flap or a string tie, depending on the type of product being packaged and the required functionality of the bag.
6. Quality Control
Quality control is a crucial step in the manufacturing process of block bottom bags. The bags are thoroughly inspected to ensure they meet the required strength, size, and durability specifications. Tests are conducted to check for any weak seams, improper folds, or inadequate sealing that could compromise the bag’s performance.
Additionally, the bags are checked for uniformity in printing, ensuring that the design and text appear as intended. Some manufacturers also perform load tests to ensure the bags can hold the weight of the intended product.
7. Packaging and Shipping
Once the block bottom bags pass quality control, they are packed and prepared for shipment. The bags are stacked in bundles or rolls, depending on the packaging requirements. The bags are then ready for delivery to businesses across various sectors, including food, chemicals, and retail.
The finished bags are shipped in bulk to wholesalers, retailers, or direct users. Efficient logistics and careful handling ensure that the bags arrive in good condition, ready to be used for product packaging.
Conclusion
The manufacturing process of block bottom bags in India involves a series of intricate steps, from material preparation to final quality control. These bags, whether made of paper, plastic, or composite materials, offer businesses a reliable and cost-effective packaging solution. With advances in technology and a growing demand for sustainable packaging, Indian producers continue to innovate, making block bottom bags an essential part of modern packaging solutions.
As industries continue to focus on reducing their carbon footprint, block bottom bags made from eco-friendly materials are likely to see increased adoption. With a combination of durability, functionality, and customization options, block bottom bags will remain an important packaging choice for Indian producers for years to come.