In today’s environmentally conscious world, businesses and industries are increasingly adopting sustainable practices to reduce their carbon footprint and waste. One of the most effective ways to achieve this is through the use of reprocessed materials, including BOPP (Biaxially Oriented Polypropylene) bags. These bags are commonly used in packaging, from food and agriculture to retail and industrial sectors. However, like many plastic products, BOPP bags have a significant environmental impact. The solution? Reprocessing.
In this blog post, we will take you through the lifecycle of a reprocessed BOPP bag, showing how waste can be transformed into a new, functional product, reducing environmental harm and promoting sustainability.
What Are BOPP Bags?
Before diving into their lifecycle, let’s first understand what BOPP bags are. BOPP is a form of polypropylene (PP) that is stretched to create strong, flexible, and durable plastic films. These bags are popular due to their ability to offer excellent barrier properties, resistance to moisture, and durability, making them ideal for packaging a variety of products, including grains, sugar, textiles, and consumer goods.
Despite their advantages, BOPP bags contribute to plastic waste, as they are not biodegradable. This is where reprocessing becomes an important part of the solution.
The Reprocessing Journey of a BOPP Bag
The lifecycle of a reprocessed BOPP bag begins when the bag is no longer useful in its original form, either because it’s damaged, outdated, or simply no longer needed. Instead of being discarded into landfills, the bag is reprocessed and given a new lease on life. This process involves several stages, from collection to transformation into new products.
Stage 1: Collection of Used BOPP Bags
The first step in the lifecycle of a reprocessed BOPP bag is the collection of used bags. Businesses and consumers alike return their used BOPP bags to designated collection points, where they are gathered for recycling. These bags can come from a variety of sources, including agricultural packaging, retail packaging, or industrial packaging.
In some cases, businesses may partner with waste management companies that specialize in collecting and processing used packaging materials. This step is crucial as it prevents the BOPP bags from being discarded in landfills, where they would take years to break down.
Stage 2: Cleaning and Preparation
Once the used BOPP bags are collected, they need to be thoroughly cleaned before they can be reprocessed. This cleaning stage involves the removal of any contaminants such as dirt, dust, adhesives, inks, or food residue. Cleaning is important because these impurities can interfere with the recycling process and reduce the quality of the reprocessed product.
The cleaning process typically involves mechanical washing, sometimes with detergents or solvents, to remove any foreign substances from the bags. Once cleaned, the bags are sorted based on their size, color, and material composition, ensuring they are suitable for reprocessing.
Stage 3: Shredding and Melting
After the BOPP bags have been cleaned and sorted, the next step is shredding. The bags are cut into smaller pieces to make them easier to handle in the next stages. These shredded pieces of BOPP material are then melted down using specialized machines.
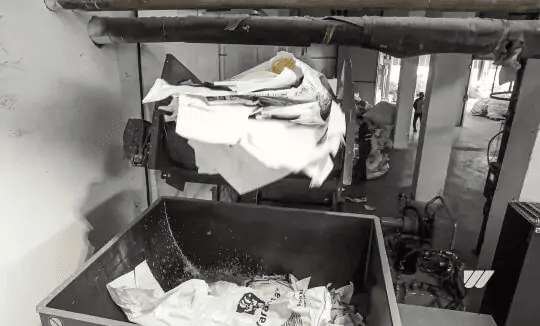
The melting process is an essential step in reprocessing, as it breaks down the plastic’s structure and turns it into a form that can be reshaped into new products. The temperature and conditions under which the BOPP bags are melted play a critical role in determining the quality of the reprocessed material.
Stage 4: Extrusion and Forming New Products
Once the BOPP material is melted, it is passed through an extruder, a machine that forces the molten plastic through a mold to form it into new shapes. This process can produce a variety of products, from new BOPP bags to other packaging materials, sheets, or films.
The reprocessed BOPP is cooled and solidified into its new shape, ready for use in a wide range of applications. This versatility is one of the key benefits of reprocessing BOPP bags—since they can be transformed into products with similar properties to the original material.
Stage 5: Quality Control and Testing
Before the newly reprocessed BOPP material is used in manufacturing new products, it undergoes a quality control process. During this stage, the reprocessed material is tested for strength, flexibility, and durability, ensuring that it meets the necessary standards for use in packaging.
Any imperfections or flaws discovered during quality testing can result in the material being recycled again or used for different applications where high-quality standards are not as stringent.
Stage 6: Production of New BOPP Bags or Other Products
Once the reprocessed BOPP material passes quality control, it can be used to manufacture new products. In the case of BOPP bags, the material is used to create fresh, functional bags for packaging goods. These bags may be used for the same purposes as their predecessors, such as packaging food, agricultural products, or retail items.
Alternatively, the reprocessed BOPP can be used to make other products like non-woven fabric, industrial packaging, or even building materials.
Stage 7: Distribution and Use
The final stage in the lifecycle of a reprocess BOPP bag is its distribution and use in the market. Just like new BOPP bags, these reprocessed bags are distributed to businesses and consumers who need them for packaging purposes. The key advantage here is that these bags come with a much lower environmental impact, as they are made from recycled materials instead of raw plastics.
Stage 8: End of Life (Again)
Eventually, these new reprocessed BOPP bags will reach the end of their life cycle, but thanks to the reprocessing process, they won’t end up as waste in a landfill. They can be collected, cleaned, and reprocessed once again, continuing the cycle of recycling and reuse.
Benefits of Reprocessing BOPP Bags
Reprocessing BOPP bags offers significant environmental and economic advantages, including reduced plastic waste and lower production costs. It also promotes sustainability by reusing materials, contributing to a circular economy.
1. Environmental Sustainability
Reprocessing BOPP bags significantly reduces plastic waste, which is one of the major contributors to environmental pollution. By reusing materials, we prevent the bags from ending up in landfills, where they would take hundreds of years to break down.
2. Cost Savings
Reprocessing BOPP bags also helps businesses save on raw material costs. The cost of producing new bags from recycled BOPP material is often lower than creating bags from virgin plastic.
3. Energy Efficiency
Recycling BOPP bags requires less energy compared to producing new plastic bags from scratch. This helps lower the overall carbon footprint of the packaging industry.
4. Contribution to the Circular Economy
Reprocessing BOPP bags supports the circular economy, where products and materials are continuously reused, reducing the need for new raw materials and minimizing waste.
Conclusion
The lifecycle of a reprocessed BOPP bag demonstrates how waste can be transformed into a valuable resource through sustainable practices. By collecting, cleaning, shredding, melting, and reusing BOPP bags, we are able to reduce environmental impact while contributing to a circular economy. This process not only provides a second life to the materials but also offers significant benefits to businesses and consumers, such as cost savings, energy efficiency, and reduced plastic waste.
As awareness of environmental issues continues to grow, reprocessing BOPP bags will play an increasingly important role in creating a more sustainable future. By embracing recycling and reusing materials, we can reduce the impact of packaging waste and make our world a cleaner, greener place for generations to come.