Selecting the right sugar bag isn’t just about holding sweetness—it’s about matching capacity, durability, and handling requirements to your operation. Whether you run a bakery, café, or large-scale food production facility, understanding the differences between industrial and retail sugar bags ensures you optimize storage, minimize waste, and maintain product quality. In this guide, we’ll explore bag types, material properties, capacity considerations, and best practices to help you make the ideal choice.
Understanding Sugar Bag Types
Sugar bags fall into two main categories: industrial-grade sacks designed for bulk handling, and retail bags intended for end consumers. Each serves distinct needs along the supply chain.
Industrial sugar bags typically range from 25 kg to 50 kg in capacity, engineered for forklift handling, palletization, and long-term storage in warehouses. Retail sugar bags, in sizes from 500 g to 5 kg, prioritize ease of carrying, shelf appeal, and resealability for home use.
Industrial Sugar Bags
Industrial bags must withstand rigorous logistics and protect sugar from moisture, pests, and tearing. They come in several material options:
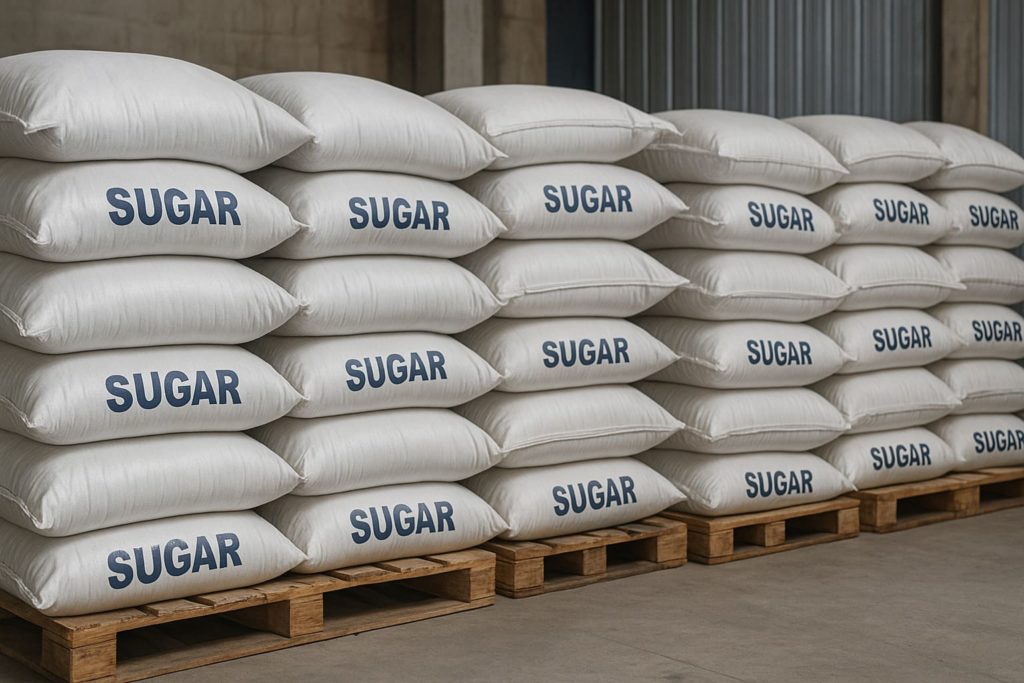
Capacity and Weight Considerations
Large-capacity bags—from 25 kg to 50 kg—reduce packaging waste and unit costs. However, their weight necessitates mechanical handling (pallet jacks, forklifts) and trained staff for safe lifting. Choose bag sizes that align with your storage space and handling equipment.
Material and Durability
Woven polypropylene (PP) bags reinforced with UV stabilizers are common industrial choices. Their high tensile strength resists punctures during transport. For extra protection, some manufacturers offer laminated liners or moisture-barrier coatings to safeguard against humidity in non-climate-controlled warehouses.
Retail Sugar Bags
Retail sugar bags focus on consumer convenience and presentation, often featuring user-friendly elements like zip closures or tear notches.
Capacity and Portability
Standard retail sizes range from 500 g for home cooks to 5 kg for small businesses. Bags under 2 kg are easy for shoppers to carry, while larger formats serve bulk buyers like cafés or catering services who prefer smaller-scale packaging than industrial sacks.
Packaging Design and Functionality
Retail bags often use multi-layer paper or plastic laminates printed with nutritional information, brand logos, and cooking tips. Resealable zip-top closures and handle cutouts enhance usability and maintain freshness, reducing the risk of clumping and insect infestation in household pantries.
Material Options Explained
Choosing the right bag material balances cost, durability, and environmental impact. Here are the most common options:
Woven Polypropylene Bags
Lightweight yet strong, woven PP bags handle heavy loads without tearing. They resist moisture penetration when laminated and can be produced in various colors and print designs. Recyclable under certain programs, they represent a cost-effective industrial standard.
Paper and Kraft Laminated Bags
Popular for retail, paper bags with polyethylene or foil lamination combine strength with barrier protection. They’re fully printable, biodegradable (paper layer), and offer moderate puncture resistance. Look for food-grade, grease-resistant linings to prevent sugar dust migration.
Jute and Natural Fiber Bags
For eco-conscious brands, jute and cotton bags offer a biodegradable alternative. Though more expensive, they provide high tensile strength and breathability—ideal for artisanal sugar producers or gift packaging. Natural fibers also convey premium, rustic branding.
Application Scenarios and Recommendations
Matching bag type to your operation ensures efficiency, safety, and customer satisfaction.
Small-Scale Bakers and Cafés
If you bake in-house or supply local cafés, 5–10 kg PP or kraft bags strike the right balance. You can rebag bulk sugar into smaller, user-friendly pouches for front-of-house use, while maintaining a larger stock reserve.
Large-Scale Industrial Users
Food processors, confectioners, and distributors benefit from 25–50 kg laminated PP sacks. Pair these with palletized storage and mechanical handling. For hygroscopic sugar grades, opt for moisture-barrier liners and climate-controlled warehouses.
Best Practices for Storage and Handling
Proper storage and handling prolong bag life and preserve sugar quality.
Humidity and Pest Control
Store sugar bags off the floor on pallets, in cool, dry environments (below 60% humidity). Implement integrated pest management—sealed bins, regular inspections, and natural repellents—especially for retail bags that end up in kitchens.
Safe Lifting and Transportation
Train staff on ergonomic lifting techniques and provide appropriate equipment (dollies, forklifts). Label heavy bags clearly with weight markings. When using retail-size bags, ensure shelf heights are reachable without overextension, reducing strain and accidents.
Read Also : The Benefits of Using Laminated PP Woven Sugar Bags for Retail Sugar Packaging
Conclusion
Choosing between industrial and retail sugar bags boils down to quantity, handling capabilities, and presentation needs. Industrial users should prioritize robust materials and large capacities for efficient bulk operations, while retail-packaged sugar demands smaller sizes, resealable closures, and attractive branding. By evaluating capacity requirements, material properties, and your operational workflow, you’ll select sugar bags that protect product quality, streamline logistics, and meet customer expectations—ensuring every granule stays fresh, secure, and ready to sweeten.