Cement bags are a crucial part of the construction industry, serving as the primary method for packaging and transporting cement. Over the years, the design and materials used in cement bags have undergone significant changes, influenced by technological advancements, environmental concerns, and the need for better efficiency in industrial packaging. In this blog, we will explore the evolution of cement bags, starting from the humble paper bag to the high-tech solutions we see today.
Early Beginnings: The Paper Cement Bag
In the early days of cement production, the packaging of cement was a relatively simple process. Paper bags were the most common material used for packaging cement. These paper bags were typically made from kraft paper, a strong and durable material known for its ability to withstand the weight of cement while offering some protection against moisture.
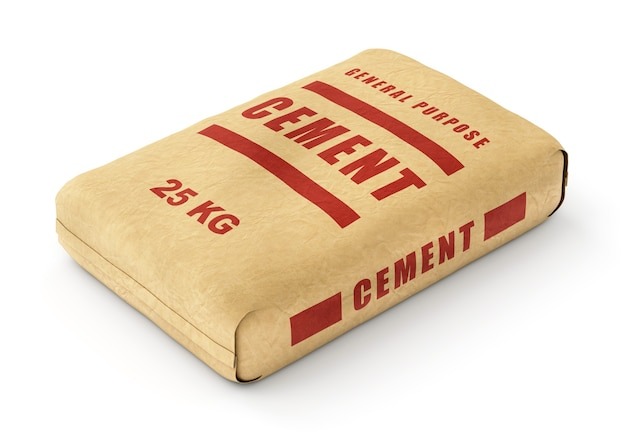
The development of paper bags revolutionized the way cement was transported and stored. Before their invention, cement was often transported in bulk or in small containers, which were not always practical or efficient. Paper cement bags allowed for easier handling, storage, and transportation of cement, making them the industry standard for many years.
The Advantages of Paper Cement Bags
Paper cement bags became the preferred choice for several reasons:
- Cost-Effectiveness: Paper was relatively inexpensive and widely available, making it an affordable option for cement packaging.
- Ease of Manufacturing: Paper bags were easy to produce and required less complex machinery compared to other materials, which contributed to lower production costs.
- Simplicity and Accessibility: The paper bag design was simple, effective, and could be easily sealed using a variety of methods, such as sewing or heat-sealing.
Despite these advantages, paper bags did have their limitations, especially when it came to durability and protection from environmental factors like moisture and rough handling.
The Transition to Plastic: A Step Forward in Durability
As the demand for cement grew and the construction industry advanced, so too did the need for better packaging solutions. Paper bags, while effective, were not always the best option in terms of durability, especially in challenging conditions. For instance, paper bags could easily tear, and the cement inside could be exposed to moisture, which could affect its quality.
This is where plastic packaging came into play. The introduction of plastic bags, particularly woven polypropylene (PP) bags, marked a significant shift in cement packaging. Plastic bags were stronger, more resistant to moisture, and offered better protection during transport and storage.
Advantages of Plastic Cement Bags
Plastic cement bags offered several benefits that made them an attractive alternative to paper bags:
- Durability: Plastic bags were far more durable than paper, capable of withstanding rough handling and resisting tearing.
- Moisture Resistance: One of the major drawbacks of paper bags was their inability to protect cement from moisture. Plastic bags provided better protection against humidity and water, which helped preserve the quality of the cement.
- Lighter Weight: Plastic bags were lighter than paper bags, which reduced shipping costs and made them easier to handle.
- Reusability: Plastic bags could be reused in some cases, providing an eco-friendlier option for certain industrial applications.
Despite these advantages, plastic cement bags also raised concerns regarding environmental impact. As plastic is non-biodegradable, the construction industry faced pressure to find more sustainable packaging options that would reduce waste.
The Rise of Sustainable Solutions
With growing awareness of environmental issues, the cement industry began exploring more sustainable packaging solutions. The focus shifted towards reducing plastic waste and finding eco-friendly alternatives that still offered the same level of protection and durability.
The Introduction of Biodegradable and Recyclable Bags
To address the environmental concerns surrounding plastic bags, some cement manufacturers began turning to biodegradable materials. These bags, often made from natural fibers such as jute or plant-based polymers, were designed to break down more easily in the environment, reducing their impact on landfills.
Another solution to the plastic problem was the promotion of recyclable cement bags. These bags, typically made from a combination of paper and plastic, could be recycled more easily than pure plastic bags. This development aligned with the growing demand for circular economy practices within the packaging industry, where materials are reused and recycled rather than disposed of.
Advantages of Sustainable Cement Bags
Sustainable cement bags offer a range of benefits for both manufacturers and the environment:
- Reduced Environmental Impact: Biodegradable and recyclable bags help reduce the long-term environmental impact of cement packaging.
- Regulatory Compliance: As governments worldwide began implementing stricter regulations on plastic waste, the cement industry sought to comply with these laws by adopting sustainable packaging solutions.
- Market Appeal: Many consumers and businesses are now more environmentally conscious, and adopting sustainable packaging can improve a company’s brand image and marketability.
While these innovations were a step forward, the search for even more advanced and efficient packaging solutions continued.
High-Tech Innovations: The Future of Cement Bags
Today, the cement packaging industry is embracing advanced technologies to create high-tech solutions that improve the efficiency, durability, and sustainability of cement bags. These innovations go beyond just the materials used; they incorporate smart technologies and more sophisticated manufacturing processes.
Smart Cement Bags
One of the most exciting developments in cement packaging is the advent of smart cement bags. These bags are embedded with RFID (Radio Frequency Identification) tags or sensors, allowing them to transmit data about the cement’s condition, location, and temperature during transport. Smart cement bags help companies track shipments in real-time and ensure the cement reaches its destination without damage or loss of quality.
Enhanced Barrier Protection
In response to concerns about moisture and other external factors that could affect cement quality, manufacturers are now incorporating advanced barrier technologies into cement bags. These bags are equipped with multi-layer coatings or specialized films that protect the cement from moisture, air, and light, preserving its quality and improving its shelf life.
Innovations in Manufacturing
Manufacturing processes for cement bags have also become more sophisticated. Automation and robotics are increasingly being used to produce cement bags more efficiently, reducing labor costs and increasing production speed. Furthermore, advances in materials science have led to the development of bags that are both stronger and more lightweight, improving both transportation efficiency and cost-effectiveness.
Conclusion: A Continuous Evolution
The evolution of cement bags has been driven by the need for better durability, efficiency, and sustainability in the construction industry. From the early days of paper bags to the introduction of plastic and biodegradable options, and now to the high-tech solutions that are shaping the future of cement packaging, the industry has come a long way.
Today, cement manufacturers face the challenge of balancing innovation with environmental responsibility. As the construction industry continues to grow, so too will the demand for packaging solutions that meet both performance and sustainability standards. The future of cement bags looks promising, with continued advancements in materials and technology paving the way for smarter, more efficient, and environmentally friendly packaging solutions.
By staying informed and embracing new technologies, the cement industry will continue to evolve, ensuring that it meets the needs of both consumers and the planet in the years to come.