In the industrial packaging world, the choice of sealing method can significantly impact the durability, functionality, and efficiency of a bag. Two common methods, heat-sealing and stitch-sealing, are widely used in manufacturing polypropylene and other industrial packaging bags. Each method offers unique features, advantages, and specific use cases that make it suitable for different industries. Understanding the key differences between heat-sealed and stitch-sealed bags can help businesses choose the right option for their packaging needs.
What is Heat-Sealing in Packaging Bags?
Heat-sealing involves using heat to bond the edges of a bag together, creating a secure seal. In this process, the packaging material, often made of plastic or polypropylene, is exposed to controlled heat, causing the material to melt and fuse. Once cooled, the edges form a solid seal that is resistant to leaks and tears.
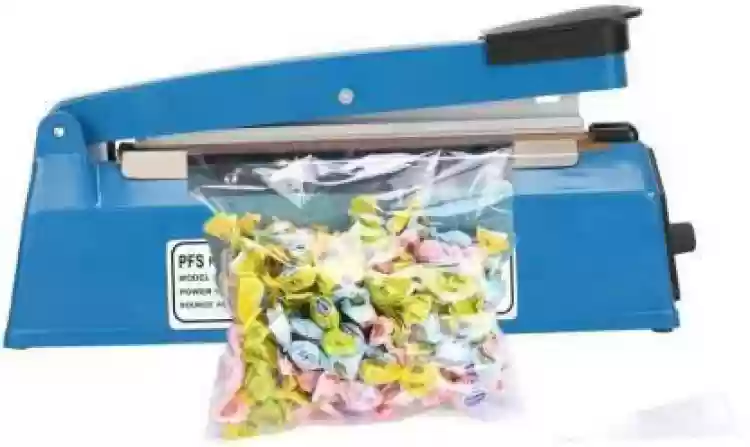
Key Features of Heat-Sealed Packaging Bags
Heat-sealed packaging bags offer several distinct benefits, making them a preferred choice for certain industries:
- Leak-Proof Seal
The most notable feature of heat-sealed bags is their leak-proof seal. Since heat fusion creates a seamless bond along the edges, these bags are ideal for storing liquids, powders, and fine particles that might otherwise escape through stitches. - Consistent and Clean Finish
Heat-sealing provides a smooth, consistent edge that gives the bag a clean, professional appearance. This feature is especially valuable for businesses focused on branding, as a uniform finish enhances the product’s visual appeal. - Ideal for Lightweight Materials
Heat-sealing is effective for lightweight packaging materials, such as thin plastics or laminated materials, that are commonly used in food packaging or small consumer goods. - Chemical Resistance
Since heat-sealed bags are made from plastic-based materials, they often have good resistance to chemicals and moisture, making them suitable for applications that require airtight seals.
Common Applications of Heat-Sealed Bags
Heat-sealed bags are popular in various industries, particularly for products that require tight seals to prevent contamination or spillage. Some common uses include:
- Food and beverage packaging for snacks, grains, and liquids
- Medical packaging for sterile items
- Powdered goods such as spices, coffee, and pharmaceuticals
- Chemical storage to prevent leaks
Heat-sealed bags are also widely used in single-use packaging where visual appeal and leak prevention are critical.
What is Stitch-Sealing in Packaging Bags?
Stitch-sealing, as the name suggests, involves using thread to stitch along the edge of the bag. This method is common in manufacturing woven polypropylene (PP) bags and other heavy-duty packaging that needs additional strength. The stitching creates a durable seam that can withstand considerable weight and pressure, making stitch-sealed bags a reliable choice for many industrial applications.
Key Features of Stitch-Sealed Packaging Bags
Stitch-sealed bags come with their own set of benefits, making them highly suitable for heavy-duty and industrial applications:
- High Strength and Durability
Stitch-sealing provides superior strength, as the stitching holds the layers of the bag together firmly. This makes stitch-sealed bags capable of carrying heavy loads without the risk of tearing or breaking. - Breathable Design
Unlike heat-sealed bags, stitch-sealed bags are typically more breathable. This allows air to circulate, which is essential for storing products that require ventilation, like fresh produce or grains, as it prevents moisture buildup and mold. - Adaptable to Heavy-Duty Materials
Stitch-sealing is compatible with thicker materials such as woven polypropylene, which is often used for packaging agricultural products, construction materials, and animal feed. - Reusability
Stitch-sealed bags are often reusable, making them an eco-friendly option. Their durability allows them to be used multiple times, which reduces waste in industries that require repeated transportation of goods.
Common Applications of Stitch-Sealed Bags
Stitch-sealed bags are widely used in industries that need sturdy packaging for bulk or heavy goods. Typical applications include:
- Agriculture for grains, seeds, and fertilizers
- Construction materials like sand, gravel, and cement
- Animal feed for livestock and poultry
- Recycling and waste management for collection and transport of materials
Their ability to carry heavy weights and withstand rough handling makes stitch-sealed bags essential for many industrial supply chains.
Heat-Sealed vs. Stitch-Sealed: Key Differences
To help you choose between these two sealing methods, here’s a breakdown of their key differences.
Durability and Strength
- Heat-Sealed Bags: These are generally more suitable for lightweight materials. While they are highly resistant to leaks, they may not be as strong when handling heavier loads.
- Stitch-Sealed Bags: Known for their durability, stitch-sealed bags can handle significant weight and rough handling without compromising on structural integrity.
Resistance to Moisture and Chemicals
- Heat-Sealed Bags: Ideal for applications requiring moisture and chemical resistance, as the sealed edges prevent leaks and keep contaminants out.
- Stitch-Sealed Bags: While strong, stitch-sealed bags are more breathable, which may allow some level of moisture to penetrate. This makes them less suitable for products that need to be kept entirely dry.
Cost and Production Efficiency
- Heat-Sealed Bags: Production tends to be more automated and faster, making heat-sealed bags a cost-effective choice for high-volume production.
- Stitch-Sealed Bags: Since stitch-sealing is often a more manual process, these bags may have a higher production cost, especially for bulk orders.
Visual Appeal and Finish
- Heat-Sealed Bags: These bags offer a clean, polished look with uniform edges, making them ideal for consumer-facing products where appearance matters.
- Stitch-Sealed Bags: Stitching can be less aesthetically pleasing but adds a rugged, functional appearance suited to industrial environments.
Choosing the Right Sealing Method for Your Needs
Choosing between heat-sealed and stitch-sealed packaging bags ultimately depends on your product requirements, packaging goals, and the conditions under which the bags will be used.
Consider Product Weight and Contents
If your product is lightweight or prone to leakage (like liquids or fine powders), heat-sealed bags may be the best choice due to their airtight properties. On the other hand, if your product is heavy or bulky, stitch-sealed bags provide the durability and strength needed to handle substantial weight.
Think About Moisture Sensitivity
Products sensitive to moisture, such as certain chemicals, medical items, or perishable food products, are better suited to heat-sealed bags that provide an airtight seal. For products that benefit from airflow, such as grains or produce, stitch-sealed bags are a better choice as they allow for some breathability.
Evaluate Reusability Needs
For industries aiming to reduce packaging waste, stitch-sealed bags are often more reusable and environmentally friendly. This makes them a suitable choice for applications requiring multiple uses, while heat-sealed bags are generally single-use.
Conclusion
Heat-sealed and stitch-sealed packaging bags each have their advantages and ideal applications. Heat-sealed bags excel in providing airtight, leak-proof packaging for lightweight and moisture-sensitive goods, making them a staple in food, medical, and chemical industries. Stitch-sealed bags, on the other hand, are the go-to option for heavy-duty applications, offering superior strength and breathability, essential in agriculture, construction, and waste management.
Understanding these key features and differences allows businesses to make an informed choice, ensuring that their packaging solution is efficient, reliable, and suitable for their unique needs.