Woven fabric rolls have become a fundamental element in various industries, from agriculture to packaging, construction, and beyond. Their versatility, strength, and adaptability make them an ideal material for various applications. However, not all woven fabrics are created equal. One of the most significant differentiations comes in the form of coated and uncoated woven fabric rolls. Both types offer unique properties and advantages depending on the application. In this post, we’ll explore the innovations driving the use of woven fabric rolls and the benefits of choosing coated or uncoated varieties for specific needs.
Understanding Woven Fabric Rolls
Woven fabrics are produced by interweaving strips of material (often polypropylene) to create a strong, durable, and flexible fabric. These fabrics are frequently used in packaging, agriculture, construction, and other sectors where strength, resistance to tearing, and durability are essential.
Woven fabric rolls can be produced in different forms, including:
- Uncoated (Plain Woven Fabric Rolls) – These rolls consist solely of woven polypropylene without additional coatings or treatments.
- Coated (Laminated Woven Fabric Rolls) – These rolls have an additional layer of lamination or coating (typically polyethylene) applied, offering enhanced properties.
Key Features of Uncoated Woven Fabric Rolls
Uncoated woven fabric rolls offer a balance of strength and breathability, making them suitable for several applications.
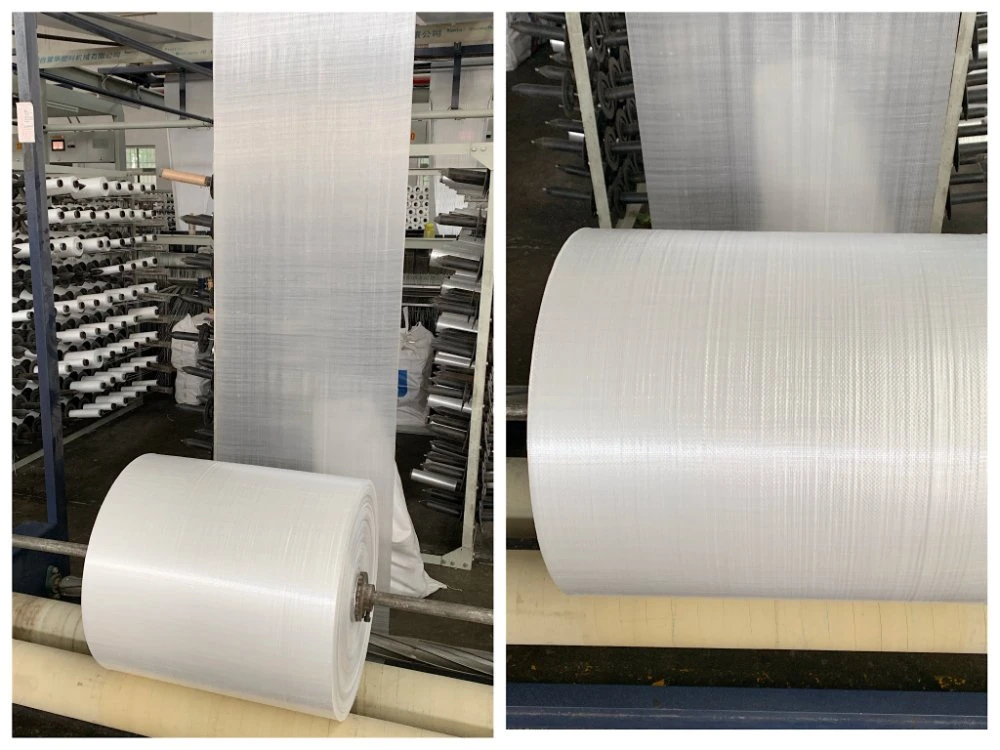
Breathability and Lightweight Structure
Uncoated fabric rolls are highly breathable, allowing air and moisture to pass through the material. This makes them an excellent choice for packaging products that require ventilation, such as grains, vegetables, and other agricultural produce. The breathability helps maintain freshness, prevent mold formation, and extend the product’s shelf life.
Because they lack additional layers of lamination, uncoated fabric rolls are lighter and more cost-effective to produce, making them a preferred option for applications where weight and cost are critical considerations.
Durability and Flexibility
Despite being lightweight, uncoated woven fabrics are incredibly durable. The interwoven structure provides impressive tensile strength, making them resistant to tearing, stretching, and punctures. They are also flexible, which allows for easy handling and shaping according to the specific needs of the application.
Uncoated woven fabric rolls are commonly used in the agriculture industry for packaging fresh produce, as well as in industries like construction where materials need to be both strong and breathable.
Innovations in Coated Woven Fabric Rolls
Coated woven fabric rolls offer an extra layer of protection that makes them suitable for more demanding applications.
Enhanced Water Resistance
One of the most significant advantages of coated woven fabric rolls is their ability to repel water. The coating, usually polyethylene, creates a barrier that prevents moisture from penetrating the fabric. This feature is especially valuable for products that must be protected from rain, humidity, or other forms of moisture. Coated fabric rolls are widely used in industries like agriculture, construction, and logistics to package products that need protection from the elements.
UV Resistance
Many innovations in coated woven fabric rolls now include UV stabilizers, which protect the fabric from degradation due to prolonged exposure to sunlight. This is crucial for products stored or transported outdoors. With UV resistance, the fabric remains durable and effective over long periods, making it ideal for outdoor storage, covering materials, or use in construction projects.
Superior Strength and Tear Resistance
While uncoated woven fabric rolls are strong, coating them further enhances their tensile strength and resistance to tears and punctures. The coating adds an extra layer of reinforcement, making these rolls perfect for heavy-duty applications. Whether used for industrial packaging or covering machinery, coated woven fabrics offer a robust solution for protecting valuable goods.
Comparing Coated vs. Uncoated Woven Fabrics
To choose between coated and uncoated woven rolls, it’s essential to consider the requirements of your specific application.
Application and Purpose
- Uncoated Woven Fabric Rolls are ideal for products that need ventilation or breathability, such as agricultural goods, fresh produce, and building materials that don’t require weatherproofing. They offer cost savings while delivering durability and flexibility.
- Coated Woven Fabric Rolls are more suited for applications where moisture resistance, UV protection, and extra durability are required. These rolls are used for heavy-duty packaging, outdoor storage, and products that need safeguarding from the elements.
Cost Efficiency
In terms of cost, uncoated woven fabrics are generally more economical due to the lack of an additional coating layer. For applications where water resistance or UV protection is unnecessary, uncoated fabrics offer a budget-friendly solution without compromising on durability.
However, the added benefits of coated woven rolls, such as water resistance and enhanced strength, may justify the higher cost for certain industries where protection and longevity are critical.
Innovations in Manufacturing and Customization
Recent innovations have significantly impacted the production of both coated and uncoated woven fabric rolls. These advancements focus on improving the performance, sustainability, and customization options available to manufacturers and end-users.
Sustainable and Eco-Friendly Fabrics
With a growing emphasis on environmental responsibility, many woven fabric manufacturers have started to incorporate eco-friendly practices into production. Recyclable and biodegradable materials are now being used to create woven rolls, helping industries reduce their carbon footprint. Furthermore, innovations in coating technologies allow for more sustainable lamination options, contributing to greener packaging and construction materials.
Customization for Industry-Specific Needs
Another significant advancement in woven rolls is the ability to customize them based on specific industry requirements. Manufacturers can now produce woven fabric rolls in various colors, widths, and thicknesses, tailored to the needs of each application. Additionally, custom printing and branding options are available, allowing companies to display their logos or product information directly on the fabric rolls.
Strengthened with Additives
In response to market demand for more durable and long-lasting woven fabrics, manufacturers have begun using special additives in their coatings. These additives improve not only UV resistance but also flame resistance and anti-static properties. This is particularly important in industries where safety regulations require fire-resistant or static-dissipating materials, such as construction, mining, and chemical manufacturing.
Choosing the Right Woven Fabric for Your Needs
The decision between coated and uncoated woven fabric comes down to the specific requirements of your project or application. Consider the following factors when making your choice:
- Environmental conditions: If your product will be exposed to moisture, UV rays, or harsh weather, coated woven fabrics are a better choice.
- Ventilation needs: For products that require airflow, such as fresh produce, uncoated woven fabrics are ideal.
- Budget constraints: If cost-effectiveness is a priority and weather protection is not needed, uncoated fabrics offer durability at a lower price.
Conclusion
Woven roll, whether coated or uncoated, offer a range of advantages for various industries. Innovations in both types of fabrics continue to enhance their functionality, making them more durable, sustainable, and customizable than ever before. By understanding the strengths and applications of each, businesses can make informed decisions that align with their specific needs, ensuring the best performance and value for their operations.