Masterbatches are a crucial component in industrial packaging, providing a wide range of benefits, including enhanced visual appeal, durability, and functionality. In simple terms, a masterbatch is a concentrated mixture of pigments or additives that is added to polymers during the manufacturing process to produce various packaging materials. The formulation of these masterbatches requires a precise understanding of chemistry, material science, and manufacturing techniques. In this blog, we will explore the science behind masterbatch formulations and how they contribute to the success of industrial packaging applications.
Understanding Masterbatches
Before diving into the science of masterbatch formulations, it’s important to understand what a masterbatch is. A masterbatch is essentially a carrier resin that holds a concentrated amount of pigment, additive, or filler. This mixture is then blended with a base resin to form a polymer material that exhibits the desired properties, such as color, texture, or enhanced functionality.
Masterbatches are primarily used in the production of industrial packaging materials, such as plastic bags, containers, bottles, films, and more. They are an essential part of the packaging industry, offering manufacturers an easy and efficient way to achieve consistent quality and performance in their products.
Key Components of Masterbatch Formulations
Masterbatches are made up of several key components, each contributing to the overall performance of the final product. These components include:
Pigments and Dyes
The primary function of a masterbatch is to provide color to the packaging material. Pigments and dyes are the coloring agents added to the masterbatch to achieve a specific shade or hue. Pigments are solid, insoluble particles that provide the color, while dyes are soluble compounds that impart color by dissolving in the polymer. Pigments are commonly used in masterbatches because they are more stable, lightfast, and resistant to heat, making them ideal for industrial applications.
Additives
Additives are substances that enhance the functionality of the polymer. These can include stabilizers, UV protectants, antioxidants, flame retardants, and plasticizers. Additives are carefully selected based on the intended use of the packaging material. For example, UV stabilizers help protect the packaging from sunlight-induced degradation, while antioxidants prevent oxidation and extend the shelf life of the product.
Fillers
Fillers are materials that are added to the masterbatch to modify the properties of the polymer. They can be used to increase the bulk of the material, reduce production costs, and improve mechanical properties such as strength and stiffness. Common fillers used in masterbatches include talc, calcium carbonate, silica, and glass fibers. Fillers are often used in combination with other additives to improve the overall performance of the packaging material.
Carrier Resin
The carrier resin is the base material that holds the pigments, additives, and fillers together in the masterbatch. It is a polymer resin that is typically selected based on the final product’s requirements. For example, polypropylene (PP), polyethylene (PE), and polyvinyl chloride (PVC) are commonly used as carrier resins in the packaging industry. The carrier resin helps distribute the pigments and additives evenly throughout the polymer, ensuring consistent color and performance.
The Formulation Process
The formulation of masterbatches is a highly controlled process that involves blending various components in specific ratios to achieve the desired results. The process typically consists of several stages:
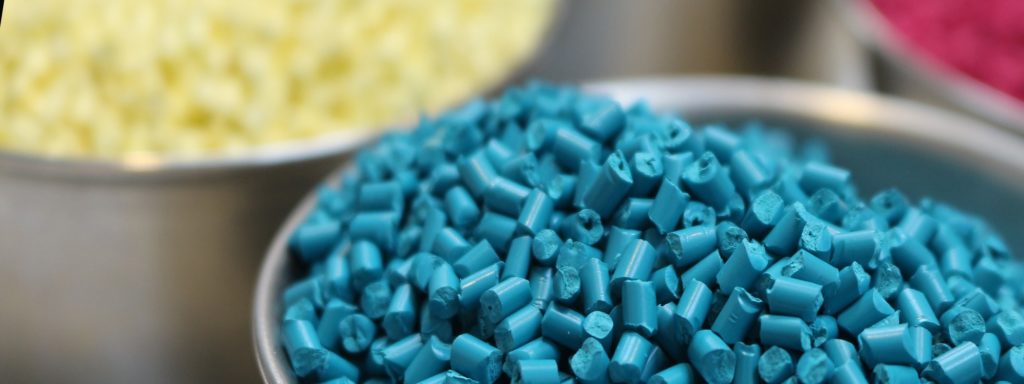
1. Selection of Raw Materials
The first step in formulating a masterbatch is selecting the appropriate raw materials. This includes choosing the right pigments, additives, fillers, and carrier resins based on the application requirements. For example, if the packaging needs to be resistant to UV degradation, a UV stabilizer would be included in the formulation. Similarly, if the packaging needs to be rigid and strong, fillers such as calcium carbonate or glass fibers may be added.
2. Pre-Dispersion
Once the raw materials have been selected, they are pre-dispersed to ensure uniform distribution. Pre-dispersion is a crucial step, as it prevents clumping of the pigments or additives and ensures that they are evenly distributed throughout the masterbatch. This is typically achieved using a high-speed disperser or a two-roll mill.
3. Mixing and Extrusion
After pre-dispersion, the materials are mixed together to form the masterbatch. This is typically done using an extrusion process, where the raw materials are fed into an extruder, a machine that melts and blends the ingredients together under controlled heat and pressure. The molten mixture is then cooled and pelletized into small granules that are easy to handle and process.
The extrusion process is critical to the quality of the masterbatch, as it ensures that the pigments, additives, and fillers are evenly distributed within the carrier resin. The extruder’s temperature, pressure, and speed are carefully controlled to achieve the desired characteristics of the masterbatch.
4. Testing and Quality Control
Once the masterbatch has been formulated, it undergoes rigorous testing to ensure that it meets the required specifications. This includes testing for color consistency, dispersion, melt flow, mechanical properties, and overall compatibility with the base resin. Quality control is essential to ensure that the masterbatch will perform as expected when added to the final packaging material.
The Role of Masterbatches in Industrial Packaging
Masterbatches play a crucial role in enhancing the performance and functionality of industrial packaging materials. By providing color, strength, and durability, they help manufacturers create high-quality packaging that meets both aesthetic and functional requirements. Some of the key roles of masterbatches in industrial packaging include:
1. Consistency and Quality Control
One of the main benefits of using masterbatches is that they provide a consistent and uniform color throughout the packaging material. This helps maintain product quality and ensures that the packaging meets the desired aesthetic standards. Additionally, masterbatches allow for precise control over the concentration of additives, ensuring that the packaging material performs optimally.
2. Customization
Masterbatches offer a high degree of customization, allowing manufacturers to create packaging materials that meet specific requirements. Whether it’s achieving a particular color shade, enhancing mechanical properties, or adding functional additives such as UV protection or flame retardants, masterbatches provide a flexible solution for packaging customization.
3. Cost Efficiency
Using masterbatches is often more cost-effective than adding raw pigments, additives, or fillers directly to the polymer. Masterbatches allow for precise control over the amount of coloring agent or additive used, reducing waste and ensuring that the packaging material is as efficient as possible. Additionally, the use of fillers can help reduce material costs without compromising the performance of the packaging.
4. Environmental Considerations
Masterbatches can also contribute to the development of more sustainable packaging materials. For example, eco-friendly masterbatches can be formulated with biodegradable additives, reducing the environmental impact of packaging. Additionally, using fillers can reduce the overall consumption of plastic, contributing to a reduction in plastic waste.
Conclusion
The science behind masterbatch formulations for industrial packaging is a complex and highly specialized process that requires a deep understanding of materials, chemistry, and manufacturing techniques. Masterbatches provide a convenient and efficient way to enhance the visual appeal, functionality, and performance of packaging materials. By carefully selecting the right pigments, additives, fillers, and carrier resins, manufacturers can create packaging that meets both aesthetic and functional requirements while improving cost-efficiency and sustainability. Understanding the science behind masterbatch formulations is essential for businesses looking to optimize their packaging processes and deliver high-quality products to their customers.