Packaging plays a critical role in protecting products, enhancing brand value, and influencing customer satisfaction. In the industrial and consumer sectors, packaging durability and reliability are paramount, and quality assurance (QA) in packaging is essential to achieving these goals. With a thorough quality assurance process, businesses can ensure that their packaging solutions meet high standards, reduce waste, and build trust among consumers. In this blog, we’ll explore the importance of quality assurance in packaging and how it contributes to durable, reliable, and sustainable packaging solutions.
What is Quality Assurance in Packaging?
Quality assurance in packaging refers to the systematic processes and practices used to maintain and improve the quality of packaging materials and products. The goal is to ensure that every product that leaves the manufacturing facility meets predetermined standards for durability, safety, aesthetics, and functionality. QA in packaging involves rigorous testing, inspection, and process improvement methodologies designed to prevent defects and inconsistencies.
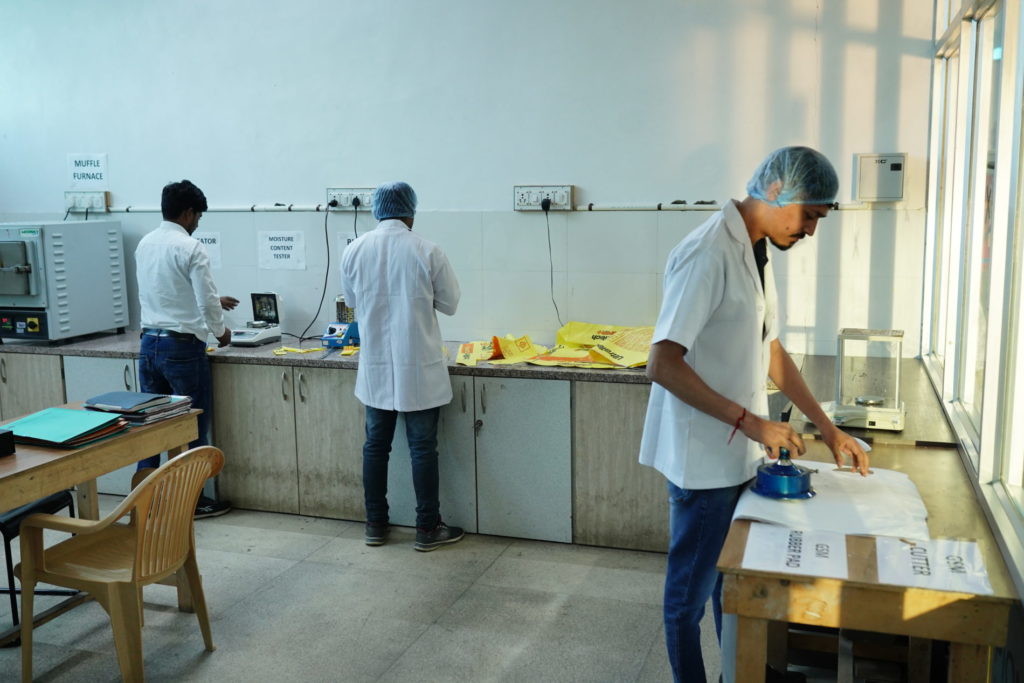
Quality assurance covers a variety of checks throughout the production cycle, from raw material sourcing to final packaging. By implementing QA protocols, packaging manufacturers can identify potential issues early in the production process, reducing waste, minimizing costs, and ensuring that products remain safe and intact throughout their lifecycle.
Why Quality Assurance is Essential for Durable Packaging
Ensuring durability is one of the primary goals of packaging. For products to remain safe and intact during storage, transportation, and handling, packaging materials must be robust enough to withstand environmental factors and physical stresses. Here’s why quality assurance is fundamental for achieving durable packaging:
- Preventing Product Damage
Poor-quality packaging increases the risk of product damage during transit, leading to financial losses and dissatisfaction for both the manufacturer and consumer. Quality assurance helps identify weaknesses in packaging materials that could compromise product integrity, allowing for adjustments before items are shipped. - Building Brand Reputation
Brands that consistently deliver products in secure, durable packaging reinforce customer confidence and brand loyalty. Packaging failures can harm a brand’s reputation, leading to negative reviews and a loss of consumer trust. Quality assurance helps maintain high standards, ensuring that products consistently arrive in top condition. - Meeting Regulatory Standards
Many industries have stringent regulations for packaging, especially in sectors such as food, pharmaceuticals, and chemicals. Quality assurance ensures compliance with these regulatory standards, reducing the risk of fines, recalls, and potential harm to end-users.
Key Elements of Quality Assurance in Packaging
Quality assurance in packaging encompasses various stages and elements to achieve optimal results. Below are some key components:
1. Material Testing
Material testing is a cornerstone of quality assurance in packaging. By assessing the properties of packaging materials, such as tensile strength, puncture resistance, and moisture barrier capacity, QA teams can determine if materials are suitable for the intended application. For example, in the case of polypropylene woven bags, testing for UV resistance is essential if the bags will be exposed to sunlight for extended periods.
2. Design Integrity
The design of packaging significantly impacts its durability. Quality assurance includes evaluating packaging design, such as seal strength, closure mechanisms, and structural integrity. Packaging must not only be visually appealing but also functionally reliable. QA ensures that design elements work together to provide sufficient protection, whether for bulk items in FIBC (Flexible Intermediate Bulk Containers) bags or for fragile products in individual packages.
3. Process Controls
Process controls are implemented throughout the production cycle to maintain consistency and quality. These include setting specific parameters for machine operations, conducting routine inspections, and following standard operating procedures. By closely monitoring each stage of production, manufacturers can prevent deviations that might compromise the quality of the packaging.
Testing Methods in Quality Assurance for Packaging
To ensure that packaging meets the required standards, manufacturers rely on a range of testing methods. Some commonly used tests include:
1. Drop Testing
Drop testing simulates the conditions packages might face during transportation, such as falls or rough handling. By dropping packaged items from various heights, QA teams can assess whether the packaging can adequately protect the product from impacts.
2. Compression Testing
Compression testing evaluates a package’s ability to withstand stacking pressure during storage or transportation. For instance, palletized goods are often stacked, and if the packaging lacks the necessary strength, items on the bottom layers could be damaged. Compression testing is crucial for maintaining product safety in stacked environments.
3. Vibration Testing
Packages are often subjected to vibration during transit, which can compromise weaker materials or poor designs. Vibration testing replicates transportation vibrations to ensure that packaging remains intact, especially for sensitive products or those with liquid components.
4. Environmental Testing
Environmental testing exposes packaging materials to conditions like humidity, extreme temperatures, and UV light to determine how they hold up over time. This type of testing is essential for products that may be stored outdoors or in non-climate-controlled settings, ensuring that they remain durable in real-world environments.
How Quality Assurance Reduces Environmental Impact
Quality assurance isn’t only about durability and reliability; it also plays a crucial role in sustainability. When packaging meets high standards, it reduces waste, decreases the need for replacements, and ultimately contributes to environmental conservation.
- Reducing Material Waste
By identifying defects early, quality assurance minimizes wasted resources, as defective products don’t reach the consumer. This reduction in waste helps conserve resources and reduce landfill impact. - Promoting Reusability and Recyclability
Durable packaging that is designed and tested for reusability can serve multiple purposes, lessening the need for single-use materials. Additionally, QA ensures that materials chosen for recyclability maintain their strength throughout their intended use. - Lowering Carbon Footprint
Efficient packaging design and durable materials reduce the overall volume and weight of packaging, leading to fewer transportation resources. This reduction in fuel consumption translates to a smaller carbon footprint for the packaging lifecycle.
Challenges in Quality Assurance for Packaging
While quality assurance brings numerous benefits, it also comes with challenges:
- Maintaining Consistency Across Large Volumes
Ensuring that all packaging meets quality standards across thousands or millions of units can be challenging. A robust QA process with automated inspections and sampling protocols is essential for maintaining consistency. - Balancing Cost with Quality
Quality assurance processes incur costs, from material testing to employee training. Companies must strike a balance between maintaining high-quality standards and managing costs effectively to remain competitive. - Adapting to Changing Regulations
As regulations evolve, especially in the realm of environmental impact, companies must continuously update their QA processes to stay compliant. This adaptation can be resource-intensive but is essential for long-term sustainability.
Future of Quality Assurance in Packaging
The future of quality assurance in packaging is increasingly being shaped by automation and technology. Innovations like smart sensors, machine learning, and real-time data analytics are revolutionizing how quality control is conducted. For example:
- Automated Quality Control
Automated systems can inspect materials and finished products with greater accuracy, increasing the efficiency of quality control while reducing human error. - Predictive Analytics
By analyzing data from previous production cycles, predictive analytics can forecast potential quality issues, allowing proactive adjustments to prevent defects. - Sustainable Material Innovations
Advances in sustainable packaging materials, combined with rigorous quality testing, will play a critical role in reducing environmental impact and enhancing durability in the future.
Conclusion: Building Trust Through Quality Assurance
Quality assurance in packaging is more than just meeting specifications; it’s about building a brand that consumers trust. By ensuring that packaging is durable, reliable, and environmentally conscious, companies can enhance their reputation, reduce costs, and satisfy customer expectations. For manufacturers and brands alike, investing in a comprehensive quality assurance strategy is essential for long-term success and sustainability in an increasingly competitive market.
Through continuous improvements and a commitment to quality, packaging companies can make a meaningful impact—both for their clients and for the environment.